受託開発の歩み
HISTORY OF CONSIGNMENT PRODUCTS
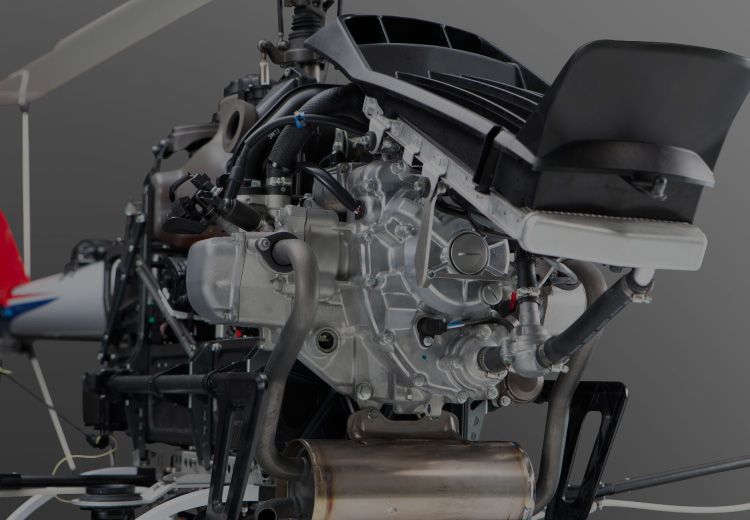
1980 - 2005
- 2006 -
1980 - 1985
各分野への技術者派遣を通じて、
R&D領域全般で礎を築く
ヤマハエンジニアリング(株)設立
(現在のヤマハモーターエンジニアリング(株))
1980
ヤマハ発動機への技術者派遣と
設計受託開始
モーターサイクルから自動車エンジン、船外機など各商材の設計部門、生産技術部門へ技術者を派遣し、人材の育成と技術の獲得を推進。ここで培った実績と人脈が、受託事業の柱へと育っていく。
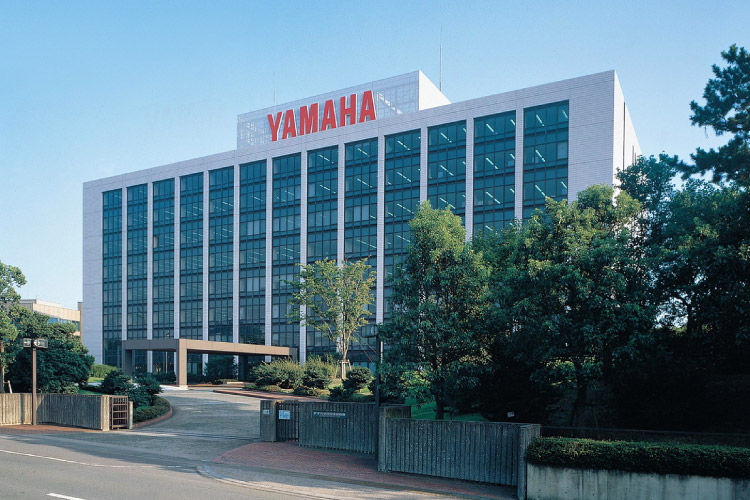
1981
ロボットコントローラー開発開始
IM事業部での制御ソフト開発受託開始。
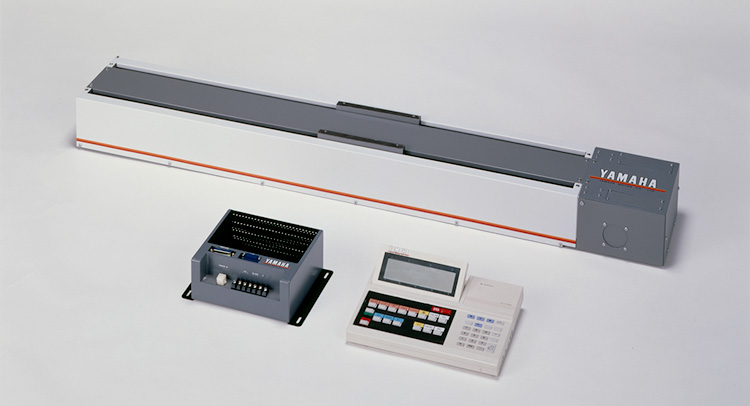
コンピューター教育/機器販売事業開始
1985
1986-1990
モーターサイクルを皮切りに、
躍進する受託開発事業
(株)ワイ・イー・シーに社名変更
1986
海外R&D開発支援開始
モーターサイクルの車両設計業務として、欧州のR&D部門から設計受託を開始。以降、継続的に海外開発拠点の開発力を補う形で技術的な開発支援を行う。(欧州、中国、ブラジルなど)
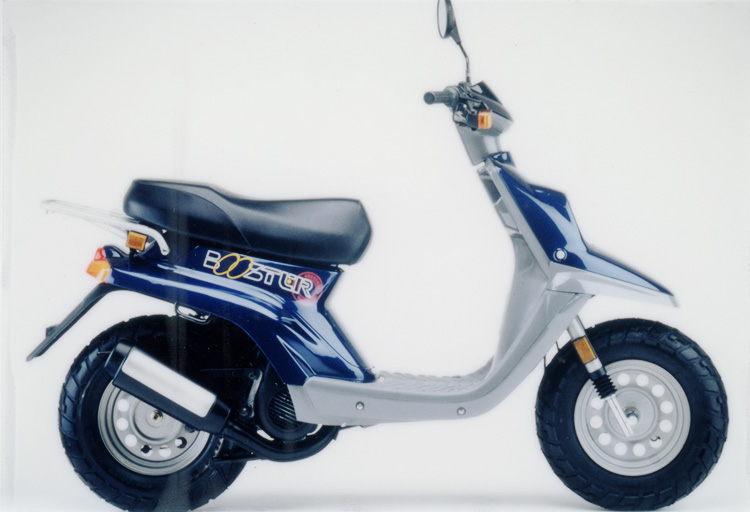
1987
無人ヘリ開発支援開始
スカイ事業部への開発支援を開始。電装設計および無線機器開発、散布機搭載などの製品化を実現。
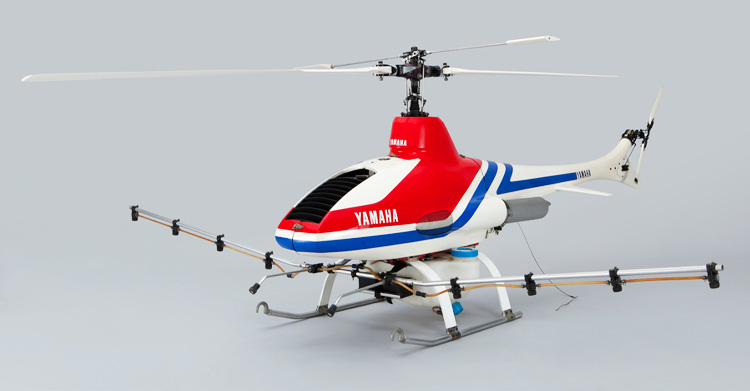
1988
鋳造バリ取りロボット開発
船外機の鋳造部品の外観仕上げ(バフ仕上)をロボット化。熟練工の技をロボットに置き換えた。
1990
レーシングカートエンジン開発支援
モーターサイクル用エンジンをベースとするレーシングカートエンジンの開発を、設計から実機評価まで通貫で実施。
シャシーに適合したコンプリート車をプロデュースして供給した。
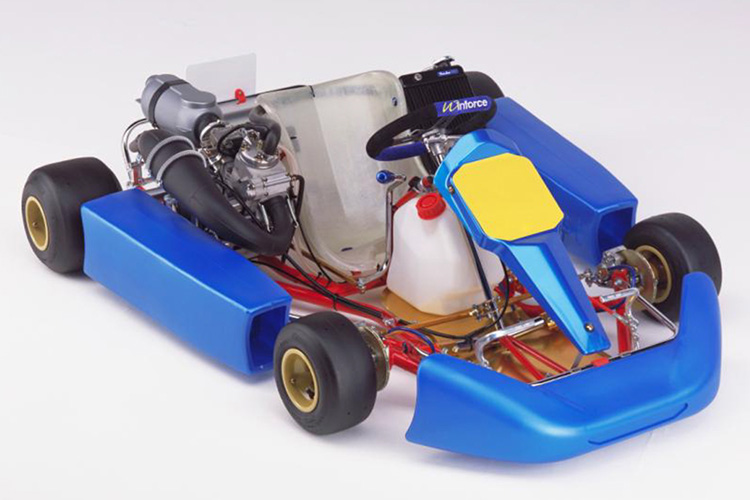
1991-1995
四輪に、マリンに、
広がるエンジン開発支援
1991
生産技術部門のホームベースとして
「テクニカルラボ」が完成
1991年6月、磐田市天龍に初の自社屋「テクニカルラボ」が完成。生産技術部門の砦となり、自動組立・搬送システムの設計開発と製作が行われた。
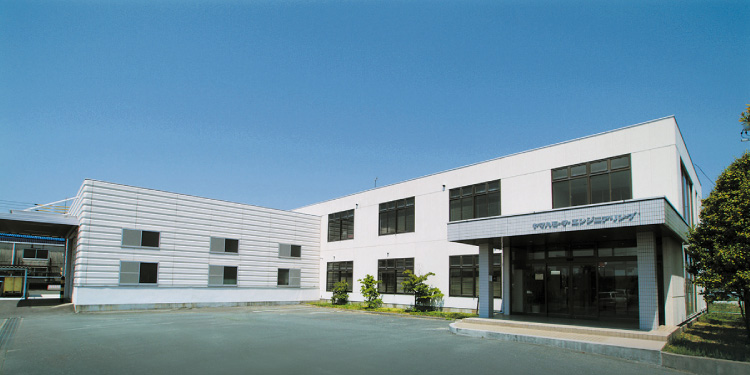
ストリートバイク開発支援開始
海外自製モデルのスクーターをメインに、車体設計の受託をチーム体制で開始。
1993
企業理念「技術を通じて社会へ貢献し、
自らの人生を有意義たらしめる」を策定
1994
1995
ダイキャスト自動化設備設計製作
ロボットを活用した自動化設備の開発を行い省人化を推進した。工法開発の内製化として当社が推進。
1996-2000
デジタル技術の進化・深化に挑む
1996
マウンター用システムソフト開発
新世代マウンターであるVISION・Windowsマウンターのシステムソフト開発受託を開始。
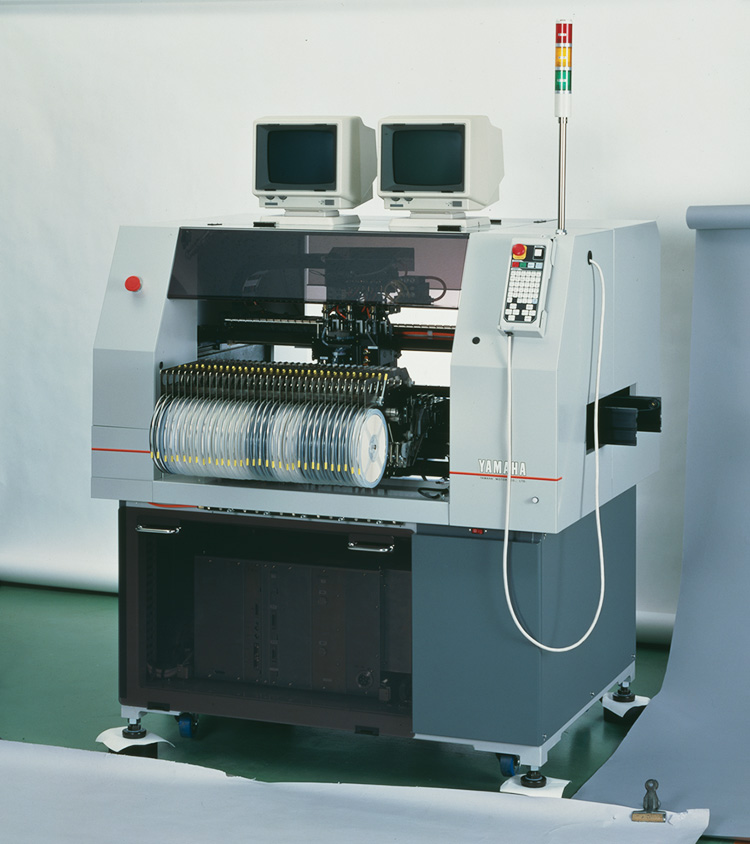
1998
3Dモデリング業務開始
生産準備系での3Dモデリング活用プロセスに合わせ、モデル作成業務の受託に着手。
1999
技術センター磐田開所
1999年1月、「技術センター磐田(現・本社)」完成。鉄骨5階建ての技術棟と同2階建ての整備棟を有するこの施設は、これまで積み上げてきた技術と業績を集約し、さらにステップアップしていくための高度なセンターとして機能させようというものであった。高速LANを張り巡らし、当時の浜松本社やヤマハ発動機と専用回線で結ぶなど、情報化時代に相応しい設備を整えた施設となっていた。
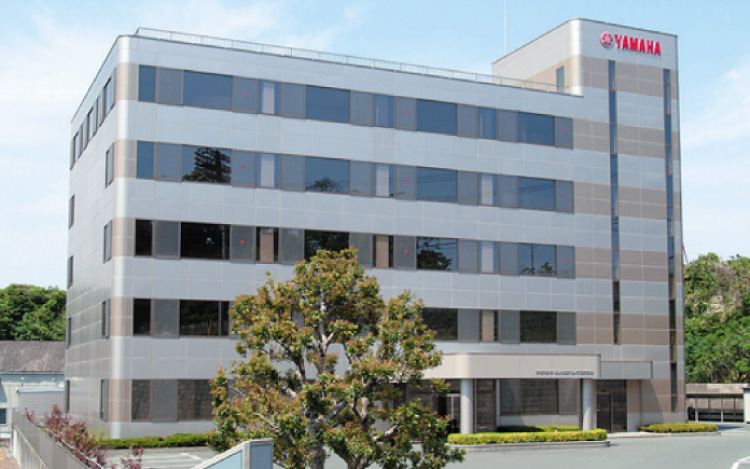
2000
ダイキャスト鋳造ロボットシステム開発
ロボットによる鋳造自動化システムをユニット化して、現地での立ち上げ期間を短縮。YMCグループ内の設備を刷新。
2001 - 2005
ヤマハ発動機のモノづくりを
世界で加速
環境マネジメントシステムISO14001認証取得
2001
本社を磐田市に移転・YEC Europe S.r.l設立
2002
デジタルエンジニアリング受託開始
ヤマハ発動機グループ内唯一のCAD業務専門部隊として、業務受託を開始。型物部品を中心とした商品開発プロセスの改革に貢献した。現在では海外パートナー企業の構築を進め、3Dモデリングを中心に業務量の拡大を続けている。
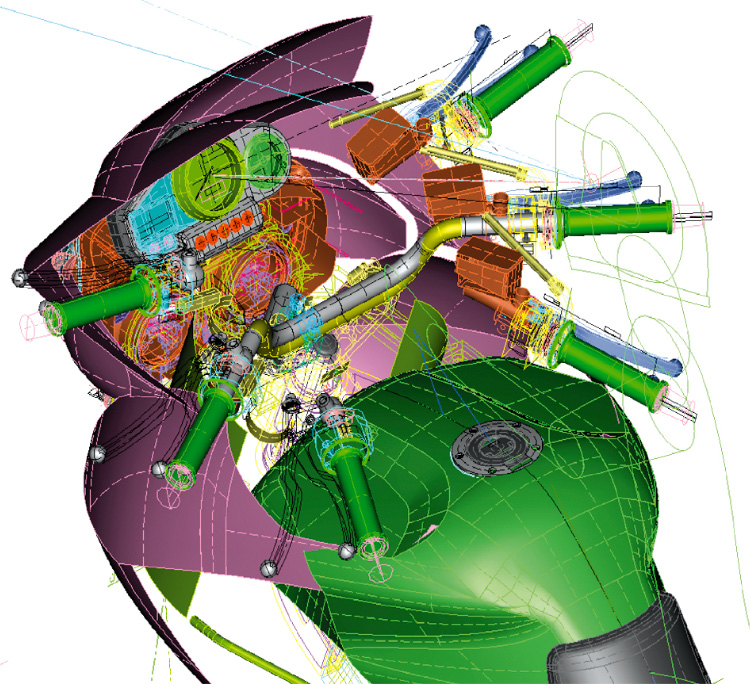
2003
燃料電池制御開発受託
DMFC(ダイレクトメタノール型燃料電池)の制御システム開発を、研究開発から受託。この制御システムを搭載した試作車「DEINONYCHIUS(ディノニクス)」は、次世代モビリティとして東京モーターショーへの出展や静岡県へのリースなどで活躍した。
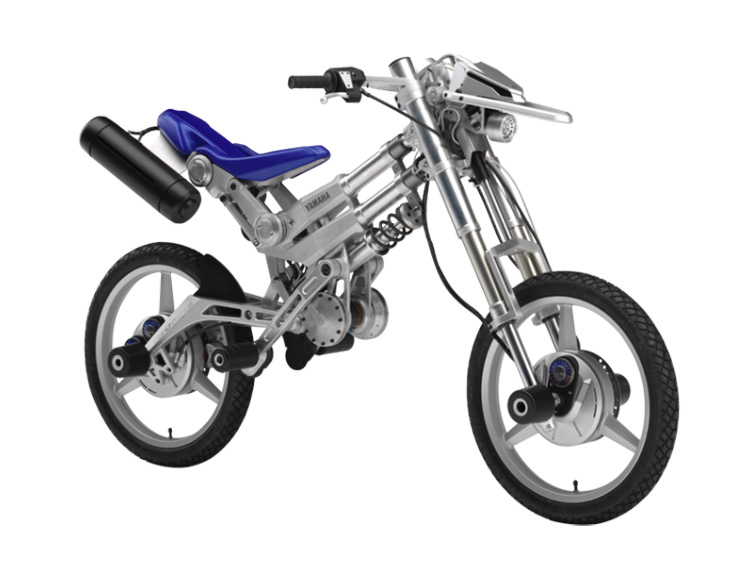
品質マネジメントシステムISO9001認証取得
2004
自動航行艇用の制御装置開発
小型電動自動航行艇(UMV)の操舵用モーター制御コントローラー開発を受託。併せて無人ビークル(UGV)の基地局の開発も行った。
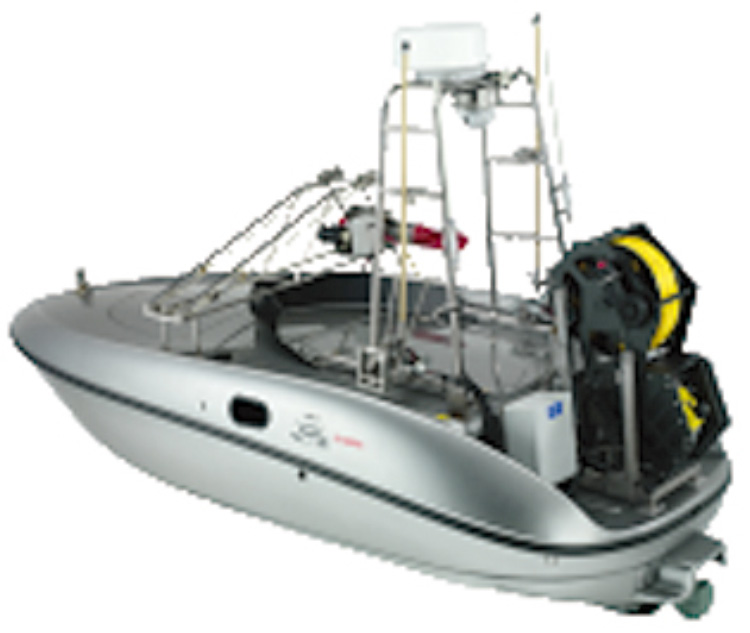
1980 - 2005
- 2006 -
1986
多軸ロボット/マウンター用コントローラー開発支援開始
ロボット・コントローラーとは、ロボットに動きを命令する制御装置。ヤマハモーターエンジニアリングは、創業間もない1981年からヤマハ発動機(株)の産業用ロボット・コントローラー開発に携わってきた。当初は単軸・2軸用のコントローラーだったが、実績が認められ、1986年からは3軸以上(多軸)のコントローラー開発の支援も開始。また、この頃から、産業用ロボットを応用したサーフェスマウンター※の開発にも携わるようになる。※サーフェスマウンターとはプリント基板に電子部品を自動装着するための装置であり、表面実装機・チップマウンターなどとも呼ばれる。
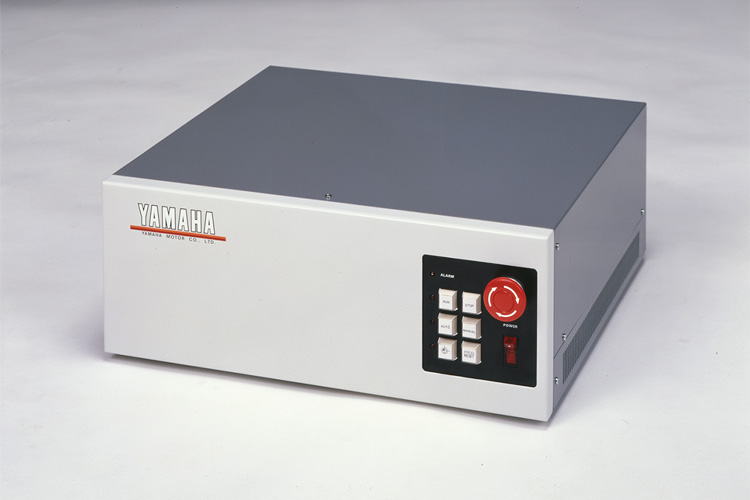
1986
エンジン組立工場設備開発(全自動組立ライン実現)
IM事業部およびヤマハ㈱のオールヤマハロボットを随所に使用したショールームラインを立ち上げ、社内外にアピールを行った。自動化による生産能力向上を実現して量産対応に貢献するだけでなく、自動組立ライン以外でも最先端ファクトリーを目指した。この理念は引き継がれ、自動組立装置および三次元搬送装置等のシステム外販の基となる。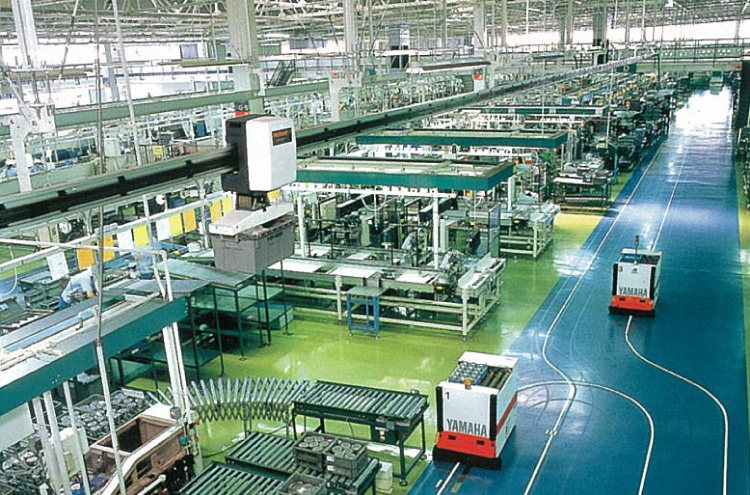
1990
PAS(電動アシスト自転車)/オフロードバギー開発支援開始
製品開発の黎明期より、機能部品の開発をチーム体制で受託していた、電動アシスト自転車PAS。それまでは「第一種原動機付自転車」とされていた動力付き自転車を「普通の自転車」として行政等に認めていただき、製品化。世界初の“電動アシスト自転車”誕生の一翼を担った。また、ATVの車体設計についてもチーム体制で受託し、Newモデルのフレームや外装樹脂部品などの設計を担当。新機種開発に貢献した。このように総合エンジニアリング力を生かした開発を通じて、ヤマハ製品の開発貢献領域を拡大していった。
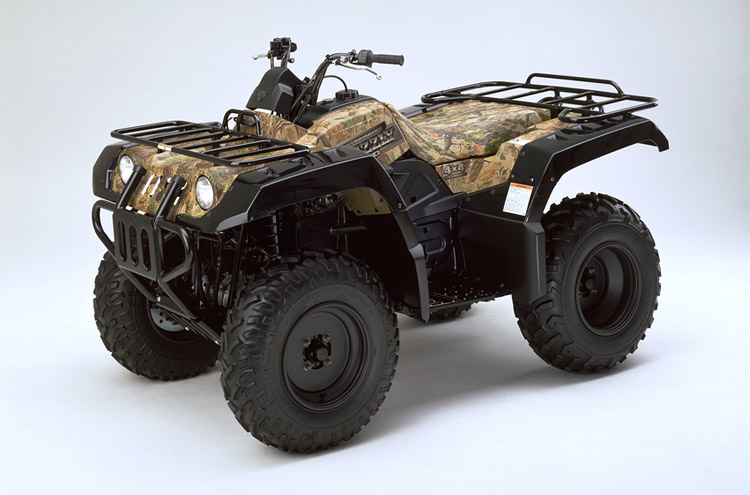
1991
自動車用エンジン開発支援開始
ヤマハ発動機(株)の自動車エンジン開発部門での経験を基に、OEMエンジンをベースに高出力化やモデルチェンジに向けた先行設計と試作をフレキシブルに受託、プロト開発のスピードアップに貢献した。またモーターサイクルのエンジンをベースとした軽量コンパクト・高回転型のスポーツエンジンを具現化するため、基本計画から設計、プロトエンジンの組立納入まで一貫して対応。
このエンジンを搭載したコンセプトカーは、国内メーカーや欧州メーカーにプレゼンされ、実際に試乗も行われた。
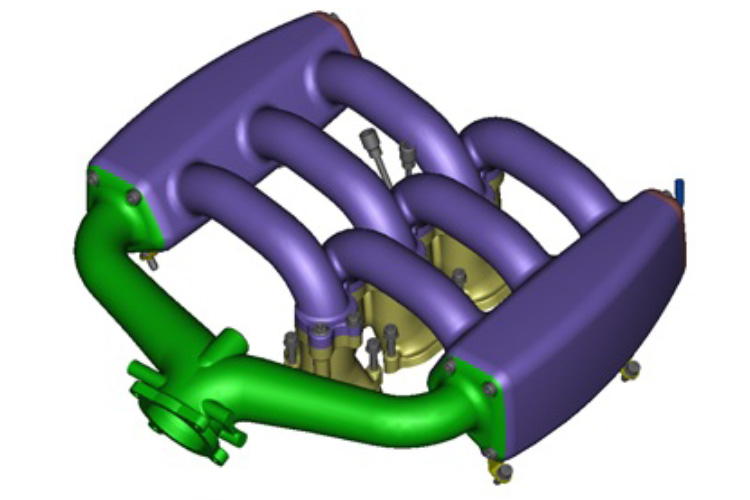
1993
船外機エンジン開発支援開始
船外機の特需仕様として空中排気仕様を開発したのが船外機エンジン開発支援の始まり。性能と水中騒音の低減との両立を達成し、そこから既存の船外機の機能改善など設計開発の受託を進めていった。やがて環境性能向上のために船外機ラインアップの4サイクル化が喫緊の課題となると、モーターサイクルや自動車用エンジンで培った当社の設計ノウハウに期待が集まる。そこで、既存のヤマハ製エンジンのユニットを活用しながら、ヘッドシリンダなど機能部品のレイアウト計画と設計を担当し、汎用エンジンベースから自動車用エンジンベースまで幅広いラインアップ構築に貢献した。
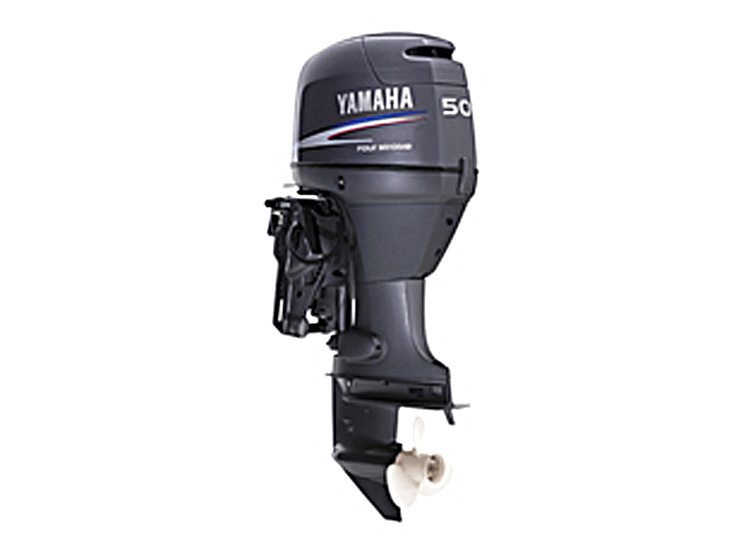
1994
中国向け低圧鋳造機製作(鋳造機内製化第1号)
グローバルな量産計画に対応するためにヤマハ発動機(株)が開発した、新しい多数個取り鋳造方案。その実現に向けて不可欠だったのが、日本で立ち上げた金型をどの国へ持っていっても同じ品質で生産できる、これまでより繊細で緻密なコントロールが可能な鋳造機──世界標準機の開発である。当社では、複雑な金型の機械的制御、温度と加圧のコントロール、等々の再現性を高め、ヤマハ品質のグローバル展開を支援。制御系をブラックボックス化して製造ノウハウの流出を抑えるなど、将来にわたる競争力の維持に努めた。
2002
アルミフレーム鋳造システム開発
当時のスポーツ系のモーターサイクルでは、商品の競争力向上のためにフレーム構造の一体化が要求されており、従来は別々に製造された部品を溶接等で組み上げ、車体で結合していた。しかしこの方法は製造工数が多く、重量の増加やコストアップに繋がる。そこで、これらのパーツを一体で成型する鋳造方案が開発された。この鋳造方案を実現するためには、デザイン性の高い意匠部品を連続して製造できる自動化システムの開発が必須だった。そこで開発したのが、当社の持つロボット等の技術を駆使した、アルミフレーム鋳造システムである。加工治具の削減を図り、ロボットによる仕上システムを構築するなど、多種少量生産に対応するシステムとした。
2003
海外向け低圧鋳造設備開発/販売
ヤマハ発動機(株)鋳造部門の海外展開が加速し、アセアンを中心とした拠点での増産に対応するべく、多くの低圧鋳造機が必要となった。そこで当社ではヤマハ発動機と共同で設備開発に取り組み、低圧鋳造機の内製化に向けて動き出した。具体な取り組みは、①グローバル標準機として設備仕様を統一 ②3D設計による事前検証の実施、手戻りロスの削減 ③コストハーフ活動(設備投資削減)、製作メーカー新規開拓(結果30%CD達成)など。
2003年から約10年間で製作されたグローバル標準機62台のうち、39台を韓国で製作して国内外の拠点へ展開。海外生産モデルのシェア拡大に貢献した。

先頭へ